OK, we all know this…but for the record…a heat pump water heater (HPWH) uses electricity to transfer heat from the surrounding air to heat the water rather than using electricity to heat the water directly. Pretty much an air conditioner that dumps the heat into a water tank rather than outside…Let me repeat that….they are air conditioners. Pretty awesome when you need air conditioning….
OK, more…let’s put a HPWH in a closet…a real closet…what are the odds? The closet gets cold….yup. What happens when surfaces get cold? OK, you now know where we are going with this….
The DOE recommends that they are installed in a space with at least 1,000 cubic feet. Assume the closet floor to ceiling height is 8 ft…the closet should be approximately 11 ft by 11 ft. Yup, happens all the time….Did I mention a “real” closet not a 125 square foot closet. A real closet gets cold.
The HPWH needs heat…it needs to be coupled to the thermal resources in the building…The best description of what is going on comes from Gary Klein and Ben Knopp. The indoor air is a working fluid that provides a HPWH with access to the thermal resources of the building. This is like water in a ground loop that provides a ground-source heat pump with access to thermal resources in the ground. Note, air, the working fluid, can deliver both sensible and latent heat.
Guess what? Danger Will Robinson…. If there is not enough working fluid or the working fluid returns before it has picked up enough heat to be useful…or if folks don’t realize air is a working fluid and they don’t let it get back to the HPWH or they send the air somewhere else…there will be issues. Robbie the Robot knew…
So let’s have a bit of fun….the HPWH discharges cold air….typically around 45 degrees F…If this impacts surfaces near the HPWH…the odds are high that the surface temperatures will be below the dew point of the indoor air…and even higher odds that the relative humidity on adjacent surfaces will be greater than 80 percent.
Ok, now let’s close the closet door so the HPWH dehumidifies the air in the closet. Problem solved? Nope. Now the risky surfaces are inside the wall cavities.
That leads us to the old philosophical question… If mold grows inside a building cavity and no one is around to see it… does it cause harm? I think we can agree that mold is not our friend.
So where are we with all this? Here goes:
-
The HPWH needs a heat source (warm air) to extract energy from and a safe place to discharge the cold exhaust air to.
-
The heat source should be able to supply heat at a rate equal to the heating capacity of the HPWH. That means exchanging air at no less than 40 cfm per 100 W (19 L/s per 100 W) of compressor power. This can be accomplished with gravity convection through passive openings, forced air exchange, or a combination of the two.
Otherwise, three things happen:
-
Air surrounding the tank gets colder, accelerating heat loss.
-
The intake air gets colder, reducing heat gain and efficiency.
-
Surfaces get colder, increasing the risks of moisture damage and mold.
-
Ductwork that could experience condensation… on the outside or inside surfaces… should be insulated and vapor sealed.
Here are a few examples demonstrating installation conditions that result in condensation on surfaces, even when following installation instructions.
See Photograph 1 - a HPWH indoor closet install. The closet is small so, in accordance with manufacturer instructions, a fully louvered door was installed, allowing new air into the closet. This HPWH has the exhaust at the back, and the air blows directly on the back wall, which happens to be an exterior wall. The installation is in Richmond, Virginia, and the new air entering the closet is both warm and has high relatively humidity. Moisture condensed on the back wall and eventually resulted in water damage and mold, affecting both the building and its occupants. The rectangle in the foreground of the closet is a dehumidifier, installed after remediation.
Photograph 1 from Nikki Krueger. HPWH Closet Installation. Cold air discharge impacts back wall. Full louvered door allows gravity convection air exchange. However, incoming air has high humidity/dew point.
See Photograph 2 – a HPWH garage install. The garage is larger than the minimum volume requirement. However, the side exhaust blew air directly at the air handler unit. You can see the outline of where it used to be. The cold exhaust air was below the dew point of the air in the garage and moisture condensed on the supply ductwork and air handler, which had to be removed to remediate the mold. This installation is also in Richmond, Virginia.
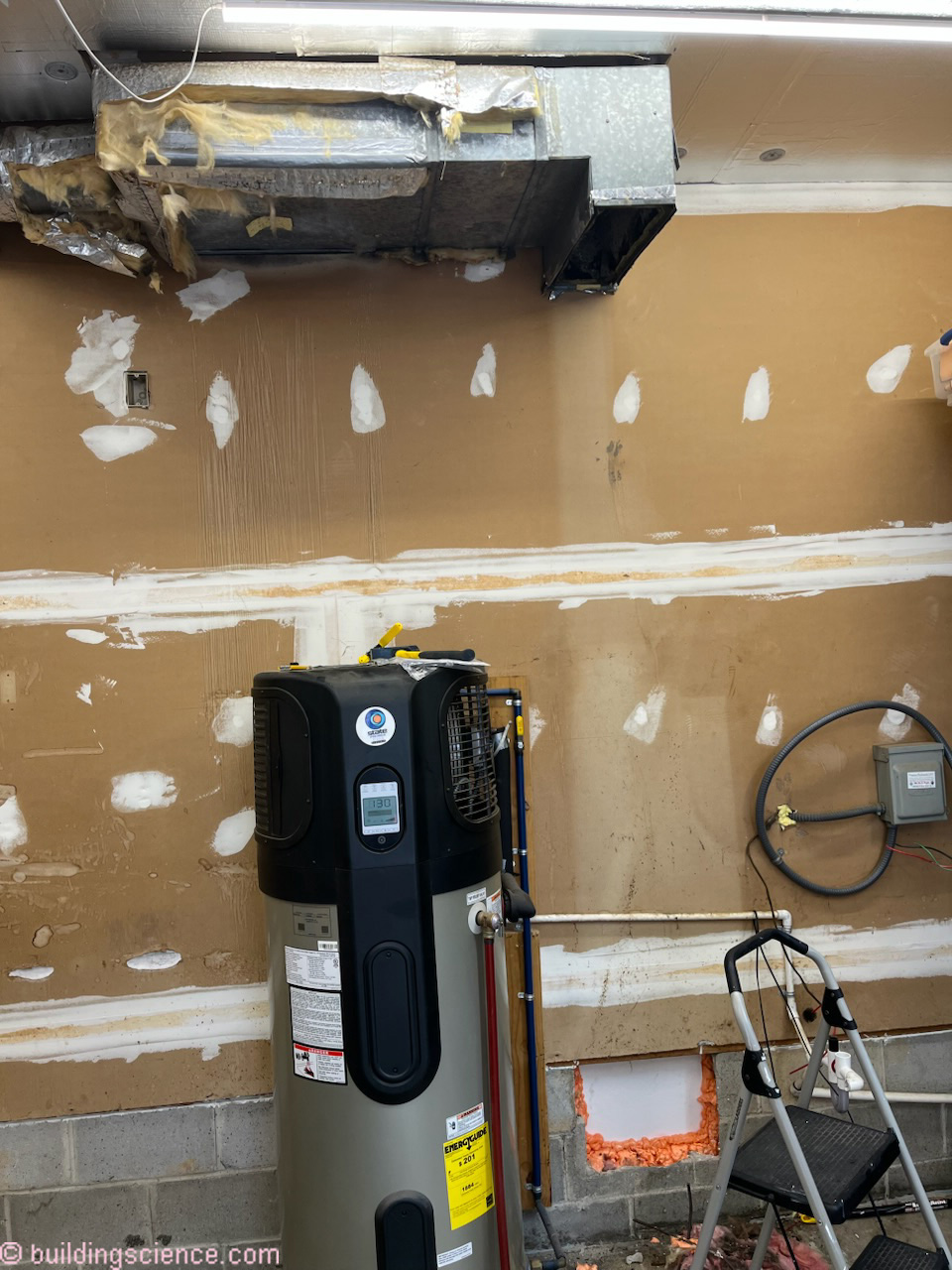
Photograph 2 from Alex DeSpain. HPWH Garage Installation. The outline of the now missing air handler unit is visible on the dry wall. Cold air discharge pointed directly at air handler. High dew point temps in garage near Richmond, VA. Condensation on air handler and supply ductwork caused mold. Equipment was removed.
See Figure 1 – a HPHW installed in an enclosed room. If there is no escape for the cold exhaust air, the temperature of the room will get colder the longer the HPWH runs. The colder the room gets, the higher the risk of condensation, especially on the cold surface facing away from the closet and towards the humid air surrounding the closet.
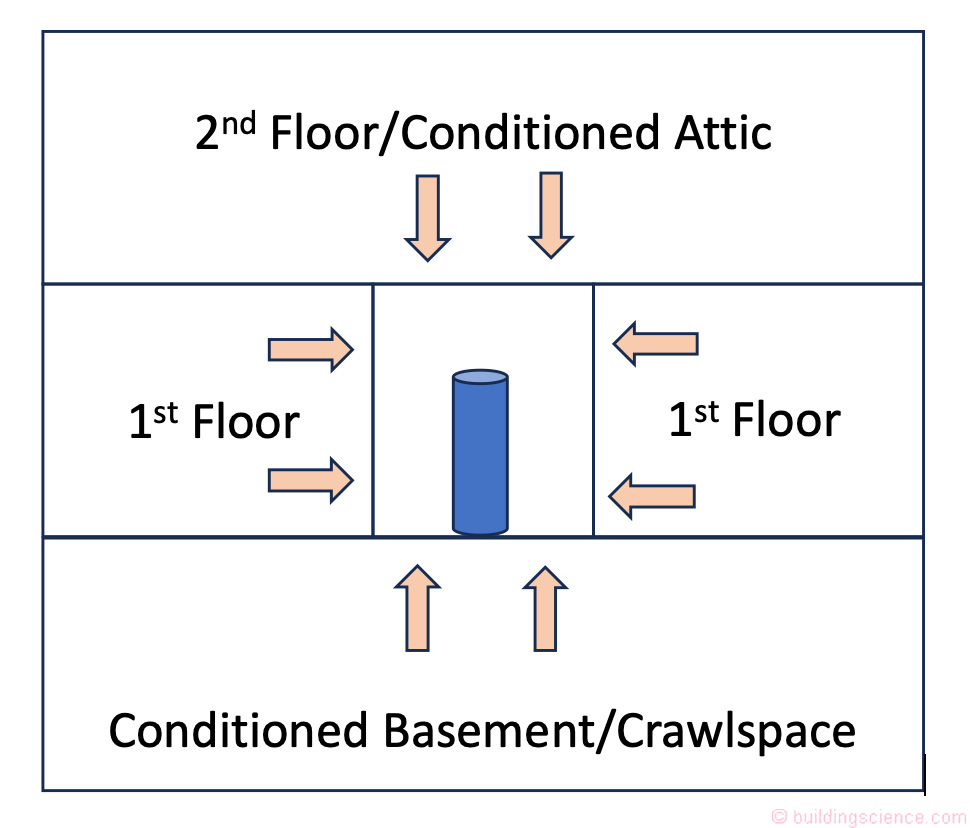
Figure 1 Indoor Closet Install. Large or small, insufficient air exchange. Indoor Air Conditions: Dry Bulb Temp 70ºF, Relative Humidity 50%, Dew Point Temp 50.5ºF. Enclosure Air Conditions: Dry Bulb Temp: 45ºF.
See Figure 2 – wall section showing the temperature gradients inside the wall. Cold air will tend to settle to the bottom and surface condensation will tend to accumulate along the bottom of the wall.
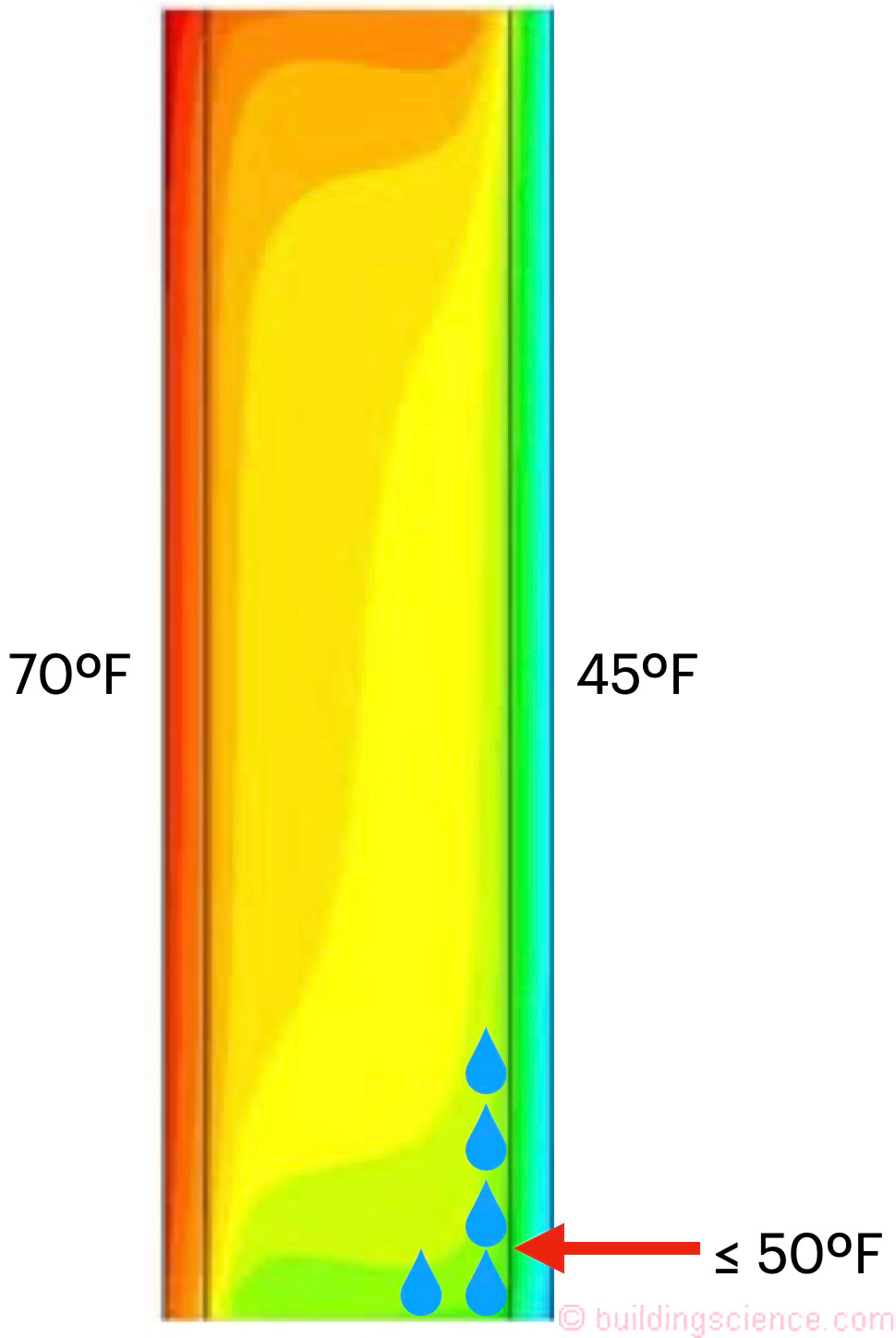
Figure 2 Close up of the Interstitial Space in the Wall. Notice the temperature gradients within the wall. Moisture will condense on surfaces below the dew point, this time hidden within the wall cavity. What if this was an external wall with insulation and some outdoor summer air leakage into the wall cavity?
The solution to preventing the formation of condensation is to not allow the exhaust air to cool any surfaces below the dew point. Mixing the exhaust air from the HPWH with enough warmer air shortly after leaving the HPWH will raise the temperature above the dew point, preventing the formation of condensation and minimizing or eliminating the risk of moisture damage and mold.
Problems When HPWH’s Go Mainstream: Gary Klein and Ben Knopp…
Although heat pump water heaters (HPWHs) have been in existence since the 1970s, their mainstream adoption occurred only in the past decade. As the technology matures beyond the initial stages of adoption, we need to assess the lessons learned. The authors have identified the following issues:
-
Inadequate heating capacity compared to advertised specifications.
-
Real-world efficiency significantly lower than rated efficiency.
-
Moisture-related damage and mold growth.
The authors believe these issues generally trace back to two primary causes:
-
Insufficient access to the thermal resources inside the building.
-
Improper handling of cold exhaust air.
Air source HPWHs are not intended to be installed in unventilated enclosures. They need access to “warm” air to operate properly as heat pump water heaters while simultaneously safely discharging the exhaust air to minimize the risk of harming the building and the occupants.
Air, the working fluid, can deliver both sensible and latent heat. When indoor air is the working fluid, the space conditioning system is never the only source of heat. Other sources include internal heat gain from people and their activities (both sensible & latent), heat gain from appliances, solar heat gain, and for some portion of the year, heat gained from air leakage and conduction through the building enclosure.
However, problems arise when the working fluid is mishandled in some way. One common problem comes when there is not enough working fluid or when the working fluid returns before it has picked up enough heat to be very useful. The other problem comes when the cold exhaust air is directed onto a surface, cooling it below the dew point of indoor air, leading to elevated relative humidity or condensation.
The first problem concerns system efficiency. One metric of efficiency is the coefficient of performance (COP) which is heat delivered to the water divided by the total electrical energy consumption, most of which comes from the compressor. In principle, all this electrical energy ends up in the water with a COP of 1. Meanwhile, the compressor is using that electricity to move additional heat from the air into the water. The sensible energy extracted from the air is based on the airflow and delta-T across the coil. The latent heat extracted from the air is based on the coil temperature being below the dew point. If the coil isn’t below the dew point, the air is not providing any latent heat.
To achieve their rated efficiency, HPWHs need unrestricted access to indoor air through natural ventilation or forced ventilation or a combination of both, at not less than 40 cfm per 100 watts of compressor power. This value is based on measured data from typical HPWHs. For example, assume the compressor of draws about 300 watts and the fan moves about 120 cfm. If the intake air is 70F, and the exhaust air is 55F (a 15F delta-T through the coil) then it can extract about 2,000 BTU/hour of sensible heat from the air. The compressor contributes about 1,000 BTU/hour of additional heat to the water. The total is 3,000 BTU/hour for a COP of 3.0. In this example, the exhaust temperature is above the dew point, so there is no contribution from latent heat.
The second problem concerns moisture damage. ASHRAE/ACCA indoor cooling design conditions are 75°F at 50%RH, which has a dew point of 55°F. However, it is not safe to assume most buildings always meet these design conditions during the cooling season. For example, measured data from hundreds of homes in a mixed humid climate show sustained indoor dew points near 60ºF for most of the cooling season. In these indoor environments, any surface that is cooled to 60ºF or below will experience high relative humidity or condensation and be at risk for moisture damage and mold. The air coming out the HPWH can be 45ºF-55ºF. Preventing this exhaust air from cooling surfaces below 60ºF can be challenging, especially in small, enclosed spaces.
The best-case scenario for installation in an enclosed space would be a closet the size of an entire house. For example, a 1625 ft² room with 8’ ceilings has an air volume of 13,000 ft³. If that volume of air enters the water heater at an airflow rate of 120 cfm (typical for many HPWHs), the HPWH would extract all the available heat in less than 2 hours (assuming no new heat is added to the air). Assume the air in the room started out at the DOE test conditions of 67.5ºF and 50%RH, passed through the HPWH once, and left the evaporator coil at 45ºF and 100%RH. The HPWH would be able to extract about 6.2 kBTU of heat from the air (5.3 kBTU sensible + 0.9 kBTU latent). This is not enough heat for a single heating cycle in a typical 3 to 4-person household of this size. Furthermore, cooling indoor surfaces down near 45ºF for more than an hour, multiple times a day, carries a high risk of moisture damage and mold in most climate zones.
If the air mass in a 1,625 ft² room does not contain enough energy to heat the water, neither will the air in a smaller room. Indoor air is not the source of heat, it is only the working fluid transporting heat to the water heater. The working fluid needs an opportunity to gather sufficient heat from one or more actual heat sources before returning to the water heater.
We ensure that gas and electric water heater installations can safely make hot water 24 hours a day, if needed; why would we limit the ability of HPWHs to do the same? HPWHs offer unprecedented water heating efficiency but they must be thoughtfully designed and installed to achieve their potential without causing harm to buildings or their occupants.